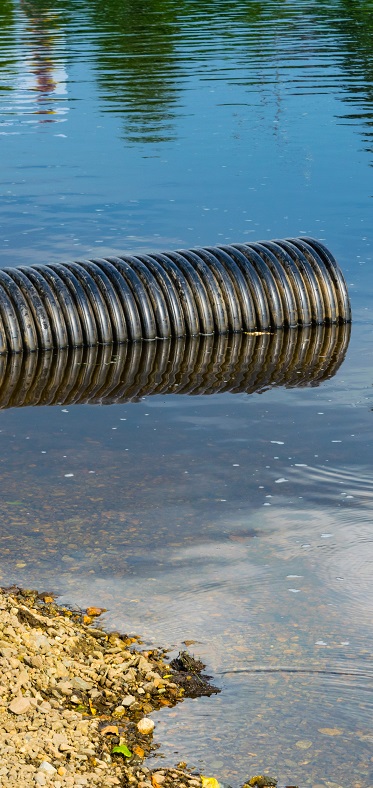
HDPE Spiral Winding Pipe
HDPE Spiral Wound Pipe
A Strong, Reliable, Cost-Effective Solution for Drainage
Benefits
A flexible pipe system that performs well in both high-cover and low-cover applications. Its unique ability to support and distribute both live and dead loads enables it to meet almost every installation condition.
Durability
Chemical inertness
High-density polyethylene is one of the most chemically inert plastics available. This inertness makes it chemical and corrosion resistant.
Abrasion resistance
HDPE pipes are resistant to abrasion giving them a significant long-term advantage over concrete and metal pipes. This also makes them reliable and secure.
Joints
Silt-tight and watertight joints mean what is inside the pipe stays inside the pipe, and what is outside the pipe stays outside. This helps protect communities, individuals, groundwater supplies, and wildlife. The integral joints on our HDPE pipes meet stringent standards set out by the EPA as well as complies with ASTM and DIN specifications.
Tolerances
Tight controls in production and the use of uniform, specified raw materials ensure our HDPE pipes are manufactured to strict tolerances. In addition, silt-tight and watertight joints perform even under moderate deflections.
Economic Advantages
Installation
HDPE pipe is light and tough, and it is manufactured in long lengths. This combination of features reduces the cost of installation.
Life Cycle Cost
HDPE pipes offer significant savings over their life cycle compared to alternative drainage systems because they are resistant to abrasion and chemicals. They have a usable service life in many typical drainage applications of 100 years.
Fittings and Accessories
Fittings are available for DN size 1000, 1200, 1400, 1600, 1800 ,2000, 2300 and 2400 mm :
- Tees/reduced tees wyes (45˚)
- Bends
- HDPE Spiral Winding pipes use helical extrusion technology.
- The manufacturing process is flexible as different sizes and stiffness of pipe can be produced using the same extrusion equipment in combination with different sizes of mandrel.
- The extruder is positioned on a carriage which passes winding stations on a track. This can take different size mandrels. The circular movement of the mandrels combined with the axial movement of the extruder result in a spiral winding of the extruded profile.
- Pipes are produced with a socket and spigot during the process. A heating wire is inserted into the socket of the pipe. After putting the socket and spigot of the two connecting pipes together, the wire is heated with the help of a special fusion device. This process welds together the two pipe ends (i.e., the socket and spigot).
- The plasticized material comes out and is cooled while being formed into a pipe.
- The pipe is cooled by a haul-off machine at a consistent rate to ensure uniform wall thickness throughout the length of the pipe.
- The pipe then passes through a saw machine and is cut to the required length.
Markets |
Applications |
|
|
HDPE Spiral Wound Pipe - A Strong, Reliable, Cost-Effective Solution for Drainage.
A flexible pipe system that performs well in both high-cover and low-cover applications. Its unique ability to support and distribute both live and dead loads enables it to meet almost every installation condition.